How To React When You Have the Hot Item
Your supply chain can play a key role in getting popular toys to customers
Key Points
- Supply chain agility and real-time visibility are crucial for managing unpredictable demand spikes and enabling faster recovery.
- Effective monitoring of component suppliers is essential to prevent production stoppages, as shortages often start at tier-one suppliers.
- Proactive weather monitoring and inventory positioning help mitigate seasonal disruption risks during peak periods.
- Warehouse efficiency can be optimized through predictive arrival data, enabling dynamic workforce adjustments.
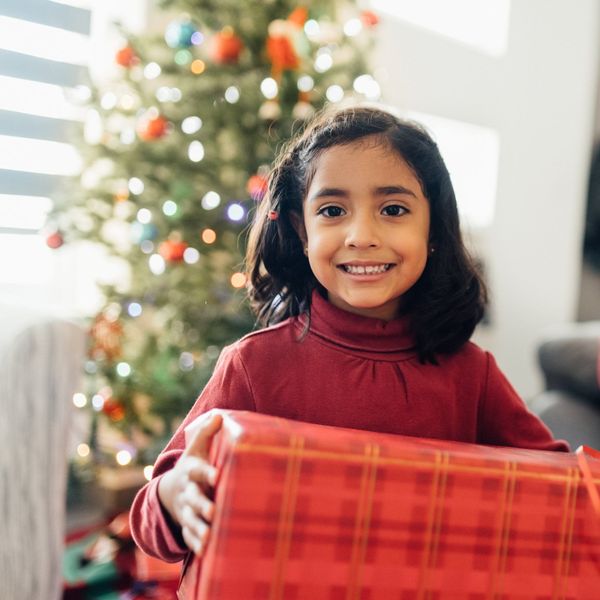
Expectations can run high during the holidays and parents are often expected to deliver the must-have toy of the season. Panic sets in if shoppers find the shelves empty, and a misalignment of supply and demand can cause even the most rational gift giver to lose perspective. What’s more, manufacturers and retailers can miss out on huge revenues due to supply shortages.
In 2024, projected hot toys include Squishmallows, Bitzee Disney Interactive Digital Pets and LEGO sets. In recent years, items such as Baby Yoda plush toys, various video game consoles and LOL Surprise! dolls have dominated wish lists, causing parents to line up outside retailers early in the morning.
For example, in 2023, the Barbie Movie Dreamhouse playset was a major hit following the success of the movie. A year earlier, in 2022, the popularity of Squishmallows, Cocomelon learning toys and the Magic Mixies Magical Misting Crystal Ball all spiked significantly. These trends highlight how unpredictable demand can strain supply chains.
Historically, shortages of popular toys have led to extreme measures, with some parents spending hundreds of dollars for a single hard-to-find toy. For instance, during Tickle Me Elmo's heyday in 1996, Tyco, the manufacturer, saw sales increase to $350 million from $70 million. Similarly, Nintendo's 1988 computer chip shortage meant the company lost what they predicted would have been 40% more game cartridge sales that year.
Ramping up production takes time, but eliminating friction in the supply chain could help those with the hot item keep production lines moving and products flowing to consumers. Here are five ways Penske Logistics helps customers gain visibility and minimize disruptions that can bring operations to a standstill.
Increase Agility
A responsive and agile supply chain is designed to handle unpredictability and move products quickly, which can ease the impact of the hot toy effect. Agility allows shippers to make changes more quickly. So even if they fall behind, they can recover much faster when compared to a rigid supply chain.
Visibility plays a key role in an agile supply chain, and Penske Logistics has developed the ClearChain® technology suite to provide real-time status updates and insights that allow shippers to make data-driven decisions and use their supply chain as a competitive advantage.
Keep Production Lines Moving
At manufacturing facilities, lost time is lost revenue, and the opportunity to capitalize on a craze may never come again. Product shortages typically result because the manufacturer’s initial forecast was off, which means its componentry supply base may not be able to fulfill demand.
A surge in a new product has a ripple effect to the Tier-One and Tier-Two suppliers. If the demand suddenly spikes, it’s often the component suppliers that struggle to meet demand and then it creates a domino effect to the manufacturer and consumer.
Through applications within ClearChain, Penske Logistics has developed a multipronged approach to optimize the supply chain, minimize disruptions and keep production lines moving.
That starts with ensuring the right orders are placed at the right time. The visibility ClearChain provides creates checkpoints throughout the supply chain, so all parties know what is needed, what is coming and when it will arrive. The systems communicate so the production facility knows if there is a discrepancy between the amount shipped and the amount needed, or if any disruptions have occurred along the way. The real-time data can also enable facilities to fine-tune production schedules and labor.
Penske Logistics also uses the technology to monitor constrained and sequenced suppliers to ensure products will move as planned. If there is concern over a specific part upsetting manufacturing activity, Penske employees can monitor these critical or late shipments.
If there is a manufacturing delay due to inbound supply issues, an efficient supply chain can help shrink the lost-sale impact. Penske Logistics has experience operating under this type of scenario and uses the supply chain to its advantage when a disruption occurs. In an organized supply chain, Penske can get components into the line as they become available, and if the manufacturer can build it, Penske can move it to the consumer. In a disorganized supply chain, the stock outages could be weeks versus days.
Keep the Supply Chain Moving
Whether users are looking at inbound information on raw materials heading into a production facility or outbound materials moving to either a warehouse or a retailer, ClearChain provides both a high-level and a detailed view of all supply chain movements to ensure nothing stops. Users can drill down into all of the information associated with an order, including the status, scheduled pickup and delivery, actual pickup and delivery, origin, destination and the part-level details of each shipment.
Even the best operation can hit a snag, but staying one step ahead of delays can keep product moving and help shippers avoid premium routing, which can add 20 to 50% to the cost of a normal route. By monitoring shipments in real-time, ClearChain allows Penske associates to identify if a shipment has fallen behind schedule. Penske’s team of experts can then work with customers to mitigate the disruption and find the best way to navigate around it or find alternative modes of transportation, if necessary.
If a bottleneck occurs on the outbound side, it is possible to rush deliveries thanks to airfreight.
Avoid Weather Delays
In many areas of the country and the globe, the holidays mean severe weather, which can create a host of problems. To increase visibility into potential disruptions, Penske monitors traffic and weather in relation to customers’ locations and carriers’ routes. This can allow associates to quickly identify areas of concern in order to get ahead in areas impacted by weather. If severe weather is predicted in advance, private fleets and supply chain partners can prepare to position product so it will be ready. That can involve pulling the product ahead so it is within the area in question or positioning it nearby so it is ready when needed.
Increase Efficiency in the Warehouse
What happens within the walls of a warehouse is a crucial component of moving product from the manufacturer to the end user seamlessly, by speeding deliveries, managing inventories and cutting costs. ClearChain tracks the flow of inventory through and around the warehouse, monitors product velocity and provides advanced notice of arrivals. Information about incoming and outbound product can be transmitted electronically between supply chain partners to increase visibility.
Increased visibility helps operators manage the workforce within the warehouse. At times, the workforce can go up as much as 30% based on picking needs. Operators can log into the system to see what is headed for the warehouse and when it is scheduled to arrive so they can schedule the appropriate labor.
Hot Toys over the Years
1952: Mr. Potato Head
1958: Hula Hoops
1959: Barbie
1960: Etch-a-Sketch
1962: Barbie's First Dream House
1963: Easy-Bake Oven
1972: Nerf Football
1977: Star Wars Action Figures
1979: Atari 2600 Game System
1980-81: Rubik's Cube
1983: Cabbage Patch Kids
1984: Transformers
1985: Teddy Ruxpin
1988: Nintendo Entertainment System
1989: Nintendo Gameboy
1991: Super Soaker
1994: Power Rangers
1995: Beanie Babies
1996: Tickle Me Elmo
1997: Tamagotchi
1998: Furby
1999: Pokémon Trading Cards
2000: Razor Scooter
2001: Bratz Dolls
2002: Beyblades
2006: Nintendo Wii
2009: ZhuZhu Pets
2010: iPad
2014: Disney Frozen Dolls
2015: Star Wars BB-8 Droid
2016: Hatchimals
2020: L.O.L. Surprise! Dolls
2021: Grogu Plush Toys
2022: Squishmallows
2023: Barbie Dreamhouse Playset