How Auto Industry Experts Prepare for the Unexpected
Technology helps you take fast action when your automotive supply chain is disrupted
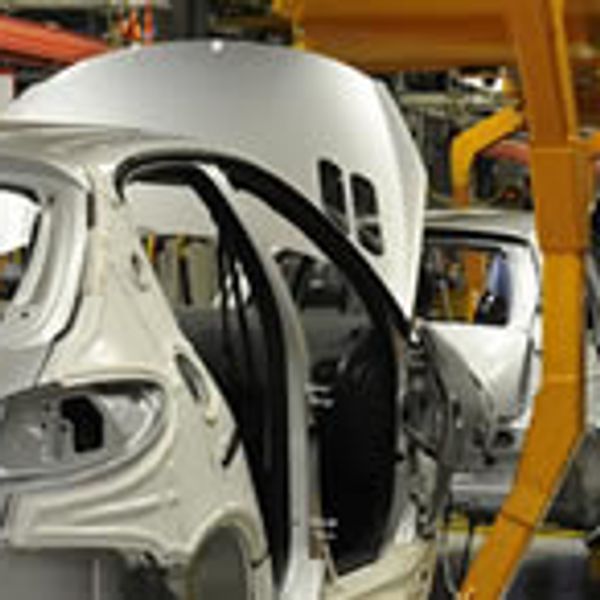
A blizzard closes a major interstate. A bridge collapse creates months of rerouting. A labor dispute closes a port. Disruptions like these create major challenges for the supply chain – especially in the automotive industry, where precision delivery windows are critical. Preparing for the unexpected can help keep your production line moving, no matter what.
In the automotive industry, ensuring parts arrive for just-in-time manufacturing is critical. Any disturbance to the production line can be catastrophic. By leveraging its ClearChain® technology, Penske Logistics can identify potential disruptions and notify automakers in advance. This allows plant managers to handle events before they become a crisis, maintain white-glove service levels and avoid missed deliveries.
Get a Control-Tower View
Since ClearChain offers a control-tower view of specific elements of your supply chain, Penske employees can monitor and manage each step in the process, from inbound raw materials to outbound finished products. This helps all parties within the supply chain pinpoint the exact location of every load, and enables a timely response to any disruption and the opportunity to mitigate its effect on the supply chain.
"The key is to try and get ahead of the event. Once we’re in the event, we try to find the best way to manage around it."
—Andy Moses, senior vice president of sales and solutions for Penske Logistics
To identify potential traffic or weather delays, ClearChain uses layered maps showing National Weather Service and Department of Transportation data. If Penske forecasts trouble ahead, data can be pulled, a geofence can be established around an impacted area and supplier information on everyone servicing that area can be obtained.
"The ability to track carriers with GPS allows us to operate like air traffic control. We can see where all of our carriers are at any point in time. The speed of information transmission lets us address problems quickly."
—Andy Moses
Respond Rapidly to Any Disruption
The track-and-trace tools integrated within ClearChain make it faster and easier to pinpoint the exact location of every load when a disruption occurs. This advanced insight helps Penske supply chain specialists connect the dots quickly, react rapidly, keep products moving and avoid premium routing when possible.
For example, if a primary mode of transportation is blocked, Penske can aid carriers in contingency planning, help shippers pull ahead materials as close to the plant or retail outlet as necessary, identify alternate routes or switch transportation modes. To keep customers in the loop, Penske issues a Red, Yellow or Green report that lists current load status and disruptions.
This type of rapid, coordinated response makes all the difference. It helps ensure manufacturing plants aren’t idle while waiting for delayed parts and the production lines continue to function at optimal capacity.
"When we know a disruption is coming, we notify our plant teams, the cross dock teams and the carriers. It helps us work as a team, and everyone does their part to make sure there is as little impact as possible."
—Andy Moses
Ensure Seamless Cross-Border Shipments
For Penske customers who require cross-border shipments, in and out of Canada or Mexico or both, contingency planning is especially important. If delays appear at a specific border crossing, Penske can shift transportation plans mid-route and send a carrier to another crossing or to another mode.
For Penske customers who require cross-border shipments, in and out of Canada or Mexico or both, contingency planning is especially important. If delays appear at a specific border crossing, Penske can shift transportation plans mid-route and send a carrier to another crossing or to another mode.
For example, Penske once experienced a potential disruption in Mexico due to a washed-out rail bridge. Penske shifted goods to over-the-road deliveries, enabling a seamless flow of product to its destination.
Managing a crisis requires both a high-level and detailed view of an entire network. ClearChain makes it possible for Penske Logistics to connect each part of the supply chain and react as quickly as possible.